When it comes to battery technology, safety is not just a feature; it’s a necessity. This is particularly true for 3.2V lithium iron phosphate (LiFePO4) cells, which are widely used in a variety of applications due to their stability and efficiency. At EVE, ensuring the safety of these cells is a meticulous process embedded in every stage of production—from supplier selection to final product testing. This blog post explores how EVE ensures the utmost safety of its 3.2V LiFePO4 cells.
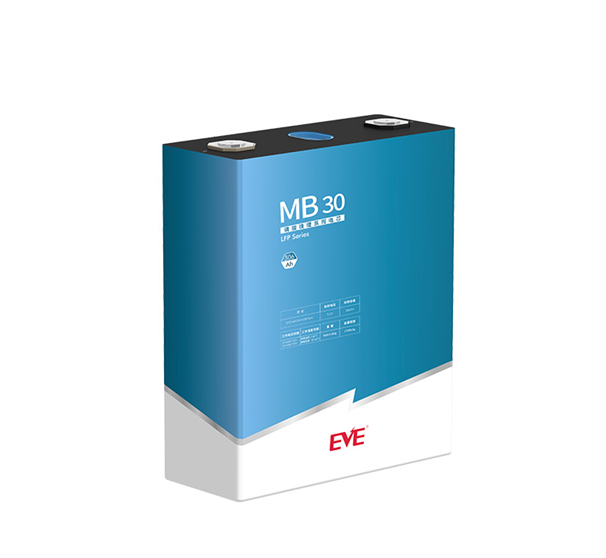
Comprehensive Supplier Onboarding and Material Testing
Rigorous Supplier Assessment
Before a supplier is even considered for collaboration, EVE conducts a thorough review and assessment of their product safety capabilities. This initial vetting process is critical as it ensures that all materials entering the production line meet EVE’s high standards for safety and quality.
Safety Testing of Incoming Materials
Once suppliers are onboarded, EVE does not simply rely on supplier assurances of quality and safety. Instead, the company conducts its own tests on incoming materials. This proactive approach allows EVE to catch and address potential safety issues before the materials are used in the manufacturing of their batteries.
Safety-Focused Design and Development
Utilization of FMEA
EVE’s product design team employs Failure Mode and Effects Analysis (FMEA) to proactively identify potential risks associated with product safety. FMEA enables the team to understand how different aspects of the battery design might fail and what the implications of such failures could be. This analysis is critical in crafting products that are not only effective but also inherently safe.
Meeting Diverse Safety Needs
The safety attributes of EVE’s 3.2V LiFePO4 cells are not determined arbitrarily. They are carefully defined based on:
– Customer Needs: Understanding what safety features are most important to the customers and how the batteries will be used.
– Product Application Scenarios: Assessing how the environments in which the batteries will be used might influence safety requirements.
– Legal Requirements: Complying with the legal standards of manufacturing locations, as well as those of regions the products will be transported through and sold in.
Design and Process Attributes
Once safety attributes are identified, they are translated into specific design and process attributes. This transformation is crucial for ensuring that every battery produced meets the defined safety criteria. Then, a detailed design plan and verification method are formulated to ensure that these safety attributes are effectively integrated into the final product.
Conclusion: Safety as a Priority
At EVE, the safety of 3.2V LiFePO4 cells is not left to chance. It is the result of a deliberate and thorough process that spans from the initial supplier vetting to the final stages of product development. By setting stringent safety standards and rigorously testing both suppliers and their materials, EVE ensures that their LiFePO4 cells are not only high-performing and efficient but, most importantly, safe for all users across various applications. This commitment to safety helps cement EVE’s reputation as a leader in the battery manufacturing industry, trusted by customers around the globe.